John E. Marushin, Managing Director & Executive Consultant
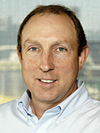
We are excited to announce John Marushin is bringing his outstanding career expertise to Lean Consulting Associates following his retirement from Alcoa.
Since 2001, John has held the position of Director, Alcoa Operations Management Consulting (AOMC) for Alcoa and is responsible for proliferating Alcoa Business System (ABS) knowledge throughout Alcoa’s 26 businesses in over 200 locations in 31 countries worldwide. Alcoa is the world leader in the production and management of primary aluminum, fabricated aluminum and alumina. Alcoa serves the aerospace, automotive, packaging, building and construction, commercial transportation, and industrial markets.
Two Bachelor of Science Degrees in Business Administration & Industrial and Systems Engineering from the Ohio State University have provided a good foundation to support business improvement in both business and operational strategy.
Trained by the Toyota Motor Corporation – Japan, as an expert in “Toyota Production System” methodology through actual projects in both North America and Japan, John’s abilities and successes did not go unnoticed, and in 1992 he was recruited by Mr. Hajime Oba to launch the Toyota Supplier Support Center (TSSC), Toyota’s internal consulting division within the United States.
Since leaving Toyota, John has developed a proven business improvement approach on how to work with people to change their work environment to Continuously Improve – driving business performance, while maintaining the target company’s identity that the enterprise was built on. While working at Toyota, as a Consultant, and a Director at Alcoa, John has been able to develop all levels of associates to become self-sufficient in implementing the Toyota production System, allowing them to use their new found skills to make their own improvements along with developing capability to train other associates to keep the company sustainable in the new system over-time. This ability to influence and inspire all levels of associates has worked as a real advantage to move companies along the change cycle and capture real dollar improvements. Using a Systems approach to change (from the customer back through the operation to the supplier) has been looked on as a key advantage to link real business requirements to actual operational changes necessary to move the total enterprise forward.
John has worked over the last twenty plus years across a diversified set of businesses from refining aluminum, to discrete part manufacturers, to service & logistics industries – implementing the Toyota Production System to improve business performance in productivity, profitability & efficiency.